Pull Release Bellcrank failure
Moderator: J D Sauser
- Tim Toberer
- Posts: 1048
- Joined: 23 Oct 2021 11:58 am
- Location: Nebraska, USA
Pull Release Bellcrank failure
I have been trying to come up with a new design for bellcranks for my pull release. My goal has been to simplify the construction, but also to make it adjustable. I thought I had it figured out only to be foiled again!
To simplify things I went to a one sided bellcrank as opposed to the Marlen style butterfly design. Instead of using a slotted stop, I switched to a one sided lock barrel, which physically attaches the rod to the BC instead of just having the BC push against the slotted stop for lowers. This eliminates making a separate slotted stop, and I found a cheap throttle stop that fits the bill perfectly. (If it only worked!) I believe this is the problem. On lowers with 2 notes on the cross shaft, as I tune one open note (with nylon nut) the the opposite finger with the other note moves as well, making it impossible to tune. Hard to explain, but on a pull release the open note is balanced by the spring and the string tension, so when you change the tension on one note, the other note self adjusts back the the original pressure it seems, finding the equilibrium.
This is hard to explain, but from what I can tell lock barrels will not work on a pull release, where you want to both raise and lower a note. I am still trying to wrap my head around this, because
it just seems like it should work, but doesn't.
My new bellcrank design would work brilliantly on an all pull design, and will still work on raise only or possibly lower only notes on a pull release I believe (which are not tuned by a nylon nut, but at the keyhead and screw stops). It is a bit crude, but easy to make and completely adjustable. I will post some pictures when I get a chance. Going All Pull would solve alot of problems, but would greatly complicate the changer design and would be much harder to build acoustic. Back to the drawing board!
To simplify things I went to a one sided bellcrank as opposed to the Marlen style butterfly design. Instead of using a slotted stop, I switched to a one sided lock barrel, which physically attaches the rod to the BC instead of just having the BC push against the slotted stop for lowers. This eliminates making a separate slotted stop, and I found a cheap throttle stop that fits the bill perfectly. (If it only worked!) I believe this is the problem. On lowers with 2 notes on the cross shaft, as I tune one open note (with nylon nut) the the opposite finger with the other note moves as well, making it impossible to tune. Hard to explain, but on a pull release the open note is balanced by the spring and the string tension, so when you change the tension on one note, the other note self adjusts back the the original pressure it seems, finding the equilibrium.
This is hard to explain, but from what I can tell lock barrels will not work on a pull release, where you want to both raise and lower a note. I am still trying to wrap my head around this, because
it just seems like it should work, but doesn't.
My new bellcrank design would work brilliantly on an all pull design, and will still work on raise only or possibly lower only notes on a pull release I believe (which are not tuned by a nylon nut, but at the keyhead and screw stops). It is a bit crude, but easy to make and completely adjustable. I will post some pictures when I get a chance. Going All Pull would solve alot of problems, but would greatly complicate the changer design and would be much harder to build acoustic. Back to the drawing board!
- Fred
- Posts: 352
- Joined: 19 Jul 2000 12:01 am
- Location: Amesbury, MA
- Tim Toberer
- Posts: 1048
- Joined: 23 Oct 2021 11:58 am
- Location: Nebraska, USA
Les Ford wrote:Pictures would be helpful
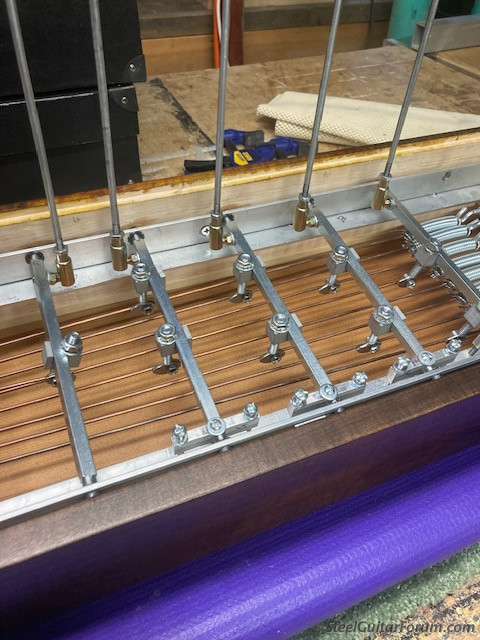
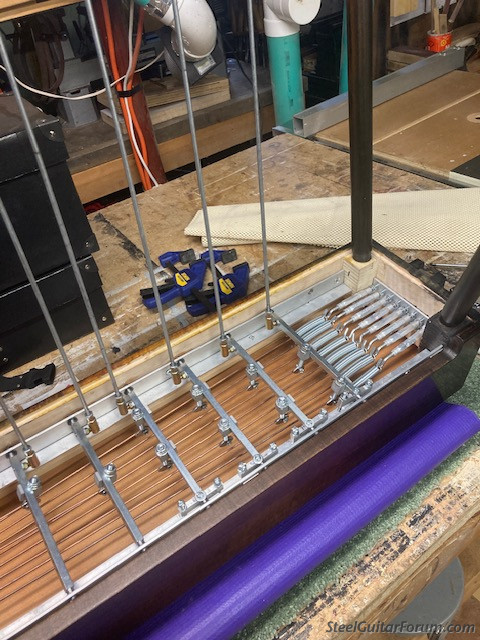
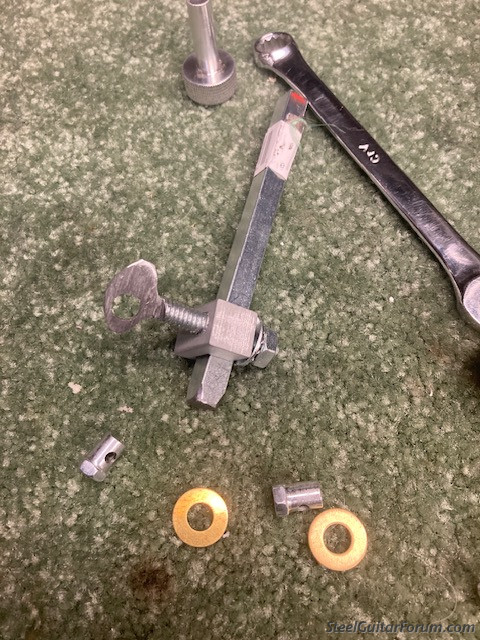
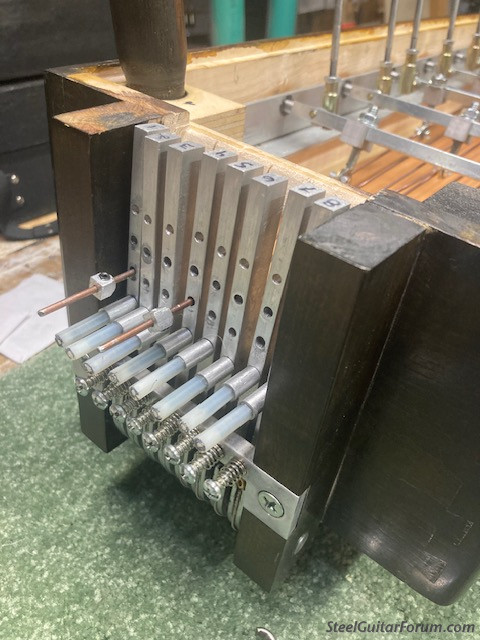
The bellcrank is just a 1/4 thumbscrew with the sides filed flat and a hole drilled for the "lock barrel". The housing is just a 5/16 slot milled just shy of 5/16 so the nut will clamp it in place. I just spent another few hours fiddling with it and am just about to give up for the day.
The 4 double lowers are on the right with the lock barrel on the spring side. The 1st raise is on the right with the lock barrel on the other side.
- Ian Worley
- Posts: 2301
- Joined: 14 Jan 2012 12:02 pm
- Location: Sacramento, CA
I'm not sure I completely understand the issue from your description, but it sounds like in general it is most likely what Fred described above. When properly set up, the only way a conventional pull release lower would exhibit the behavior you describe would be if the bell crank and cross shaft are moving/rotating as you turn the nylon to tune the open note, thus affecting other notes on the same shaft. If so you would probably just need to tighten the lower return spring(s) to hold the shaft more firmly against the neutral stop.
I'm not certain exactly how your guitar is set up, but from what I can see in the pics it looks similar to an old Marlen, with the lower return springs connected to the ends of the lowering pull rods. The first four pedals on the right are all lowers, the last two are raises, the screws on left side of the butterfly cranks along the rear apron are the neutral stops for the lowers, the right side screws are the pedal travel stops.
One other way this sort of issue could arise would be if you had more than one pedal or lever working the same pull rod, which I can't discern from the pics. In that situation the rods must be free floating with shaft collars or something similar behind the bell cranks. That sort of setup requires some additional means to tune the pulls. Since the rod is free floating you can't tighten the nylon without some addition means to hold the stop collar, like on an old Marlen or a barrel tuned Sho-Bud. The locking barrel clamps you described would not allow this.
I'm not certain exactly how your guitar is set up, but from what I can see in the pics it looks similar to an old Marlen, with the lower return springs connected to the ends of the lowering pull rods. The first four pedals on the right are all lowers, the last two are raises, the screws on left side of the butterfly cranks along the rear apron are the neutral stops for the lowers, the right side screws are the pedal travel stops.
One other way this sort of issue could arise would be if you had more than one pedal or lever working the same pull rod, which I can't discern from the pics. In that situation the rods must be free floating with shaft collars or something similar behind the bell cranks. That sort of setup requires some additional means to tune the pulls. Since the rod is free floating you can't tighten the nylon without some addition means to hold the stop collar, like on an old Marlen or a barrel tuned Sho-Bud. The locking barrel clamps you described would not allow this.
All lies and jest, still a man hears what he wants to hear and disregards the rest - Paul Simon
- Tim Toberer
- Posts: 1048
- Joined: 23 Oct 2021 11:58 am
- Location: Nebraska, USA
Thanks for the responses! I actually got it to work, sort of. So it isn't the bellcrank that was causing the issue. Which is great news! The bad news is I thought I knew how to setup my guitars, but there are some mysteries still. Acoustically it sounds like S$#!&!, but what do I expect, it is an olive can resonatorIan Worley wrote:I'm not sure I completely understand the issue from your description, but it sounds like in general it is most likely what Fred described above. When properly set up, the only way a conventional pull release lower would exhibit the behavior you describe would be if the bell crank and cross shaft are moving/rotating as you turn the nylon to tune the open note, thus affecting other notes on the same shaft. If so you would probably just need to tighten the lower return spring(s) to hold the shaft more firmly against the neutral stop.

I basically loosened everything up and went through my process again and it worked. This was the third try and took almost the whole day. I am not sure what I did differently. I think you guys are right about the return springs not being tight enough.
Another problem I found was getting the highest note to tune properly. I originally was trying to set it up with a whole step raise with a half step lower, but I found that the whole range of my changer finger wouldn't cover that. G-A raise and G-F# lower. So I had to change the whole tuning. I changed to a slightly higher gauge, but it wasn't quite enough. I guess I still have a lot to learn!
-
- Posts: 5975
- Joined: 4 Aug 1998 11:00 pm
- Location: Oceanside, Calif, USA
- Contact:
Re: Pull Release Bellcrank failure
We all do 

- Rich Cottle
- Posts: 243
- Joined: 15 Apr 1999 12:01 am
- Location: Sacramento California
- Contact:
Re: Pull Release Bellcrank failure
Yeah your always gonna have those kinds of problems with push/pull , the push/pull was the first idea that they came up with back in the 1950's , I don't know why anybody would want to use that design when the all pull is so much better
Also having those couplings and ball joints on the pedal rods is not a very good idea , it looks like you only have about 1/2" from the center of the crossbar to the center of the pedal rod , you should have 1-1/4" , remember the further from the crossbar the shorter distance it travels (Archimedes 289-212 BC), but the harder it is to push , 1-1/4" is the standard that most people have come up with
Yeah the push/pull design is kind of a pain especially with the floor pedals and the knee levers combination , the same idea works with those fingers , you have to put the pull rod holes a long ways out from the center of the finger axle and that's alright for the pulling , but like you experienced the lowering doesn't want to corroperate , especially with pedals one and two down and trying to add the E-lever or the F-Lever , they never come out right , when you lower the E's to Eb they never come back right there always sharp and the same goes with the Es to F , when you go back home there always flat , where the all pull system comes back exact if you mess with the return springs adjustment
You see the all pull system is a cantilever design and you have two or sometimes three pivot points which gives you the leverage to make it easier to push the pedals at a shorter distance , being all pull the return springs pull the cantilevers back exactly right and with a little adjusting the return springs you can get em exact
It's like I keep telling people the push/pull is obsolete and it's way too much trouble just buy a cantilever finger here on the forum and use it to make your own design , it's more work , but it's well worth it , just look at Bruce Zumsteg's design , he has worked on this problem for years and he his is one on the best there is(smooth)
And as far as bell cranks go , side mount is the best , but those are alot of work , not really you just need a drill press and you need to make a steel jig so you can make a bunch of them all the same (Mullen) has one of the best design's for bell cranks
Square or hex crossbars are much better then round , hex is eiser cause you don't need a four jaw chuck
Rich Cottle
Also having those couplings and ball joints on the pedal rods is not a very good idea , it looks like you only have about 1/2" from the center of the crossbar to the center of the pedal rod , you should have 1-1/4" , remember the further from the crossbar the shorter distance it travels (Archimedes 289-212 BC), but the harder it is to push , 1-1/4" is the standard that most people have come up with
Yeah the push/pull design is kind of a pain especially with the floor pedals and the knee levers combination , the same idea works with those fingers , you have to put the pull rod holes a long ways out from the center of the finger axle and that's alright for the pulling , but like you experienced the lowering doesn't want to corroperate , especially with pedals one and two down and trying to add the E-lever or the F-Lever , they never come out right , when you lower the E's to Eb they never come back right there always sharp and the same goes with the Es to F , when you go back home there always flat , where the all pull system comes back exact if you mess with the return springs adjustment
You see the all pull system is a cantilever design and you have two or sometimes three pivot points which gives you the leverage to make it easier to push the pedals at a shorter distance , being all pull the return springs pull the cantilevers back exactly right and with a little adjusting the return springs you can get em exact
It's like I keep telling people the push/pull is obsolete and it's way too much trouble just buy a cantilever finger here on the forum and use it to make your own design , it's more work , but it's well worth it , just look at Bruce Zumsteg's design , he has worked on this problem for years and he his is one on the best there is(smooth)
And as far as bell cranks go , side mount is the best , but those are alot of work , not really you just need a drill press and you need to make a steel jig so you can make a bunch of them all the same (Mullen) has one of the best design's for bell cranks
Square or hex crossbars are much better then round , hex is eiser cause you don't need a four jaw chuck
Rich Cottle
Last edited by Rich Cottle on 7 Mar 2025 9:15 am, edited 4 times in total.
- Tim Toberer
- Posts: 1048
- Joined: 23 Oct 2021 11:58 am
- Location: Nebraska, USA
Re: Pull Release Bellcrank failure
Thanks for your comments Rich. I totally agree with this, especially for today's extremely complex copedants. That said, the pull release still has its place, and I like the simplicity of it. I think once you get used to the idiosyncrasies, it is a great system. Also for the weekend builder with only basic shop tools, it is a good way to start building steel guitars. With patience and thought, you can get most things to work. It is best to keep it simple though.Rich Cottle wrote: 4 Mar 2025 1:30 am Yeah your always gonna have those kinds of problems with push/pull , the push/pull was the first idea that they came up with back in the 1950's , I don't know why anybody would want to use that design when the all pull is so much better
Rich Cottle
I am still experimenting with a lot of the variables and for context my copedant is nothing like the E9, but a bit like C6. My basic tuning uses only 1/2 step raises, and 1/2 step lowers. This is the first time I tried to incorporate a whole tone raise, and it caused some problems, but it seems to be working now. When I started this thread I had no idea why this thing wasn't working. Its funny cause I should re name this thread to pull/release bellcrank success

Totally agree about square over round cross shafts. I have a 4 jaw self centering chuck so no problems there.
The 1 1/4 distance from the cross shaft may be standard, but this is another place where you can experiment with the playing feel of the guitar. I have found it isn't that critical.