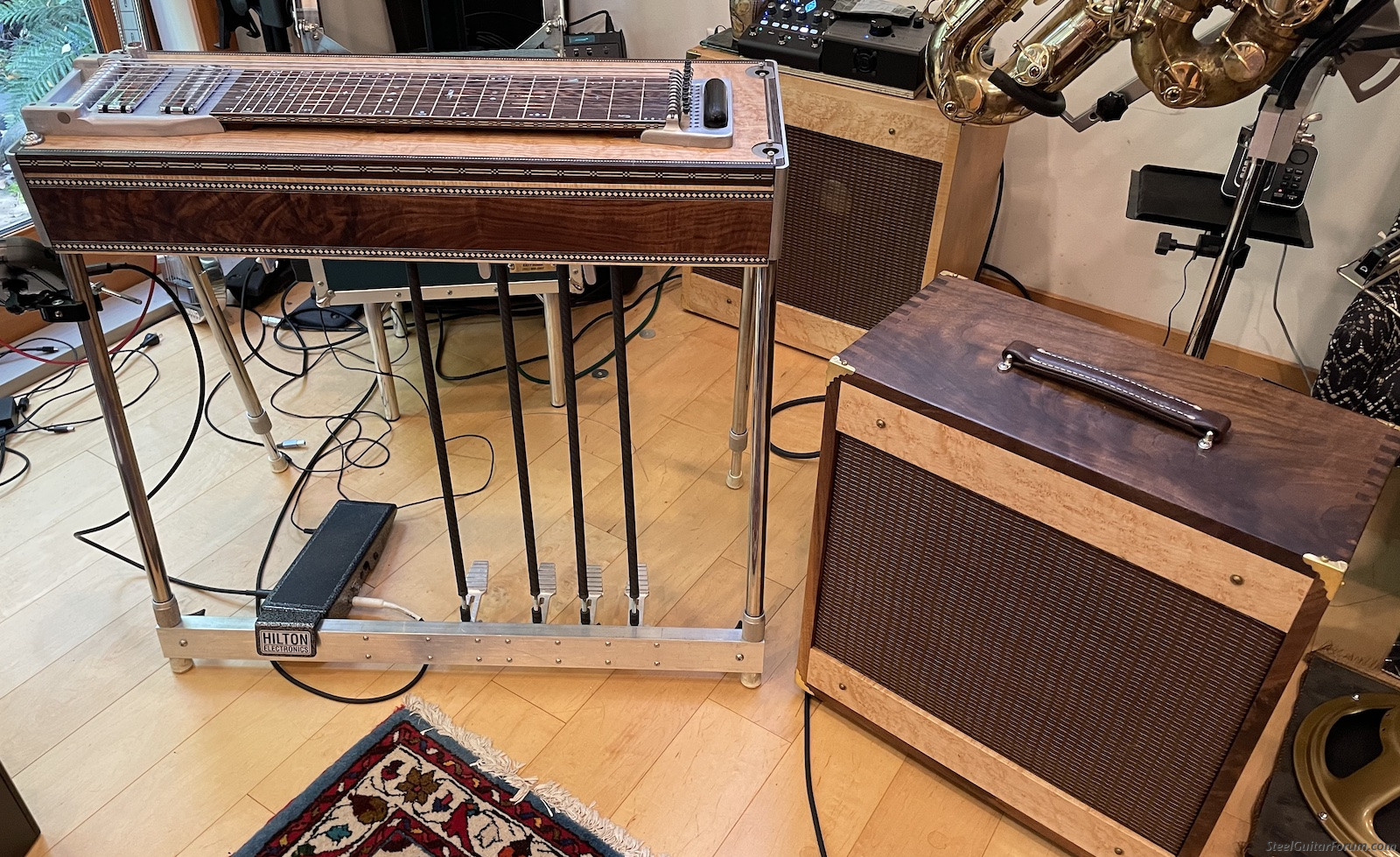
This one has sockets for a microphone boom stand. It also has 3/8 inch string spacing at the changer as well as at the nut.
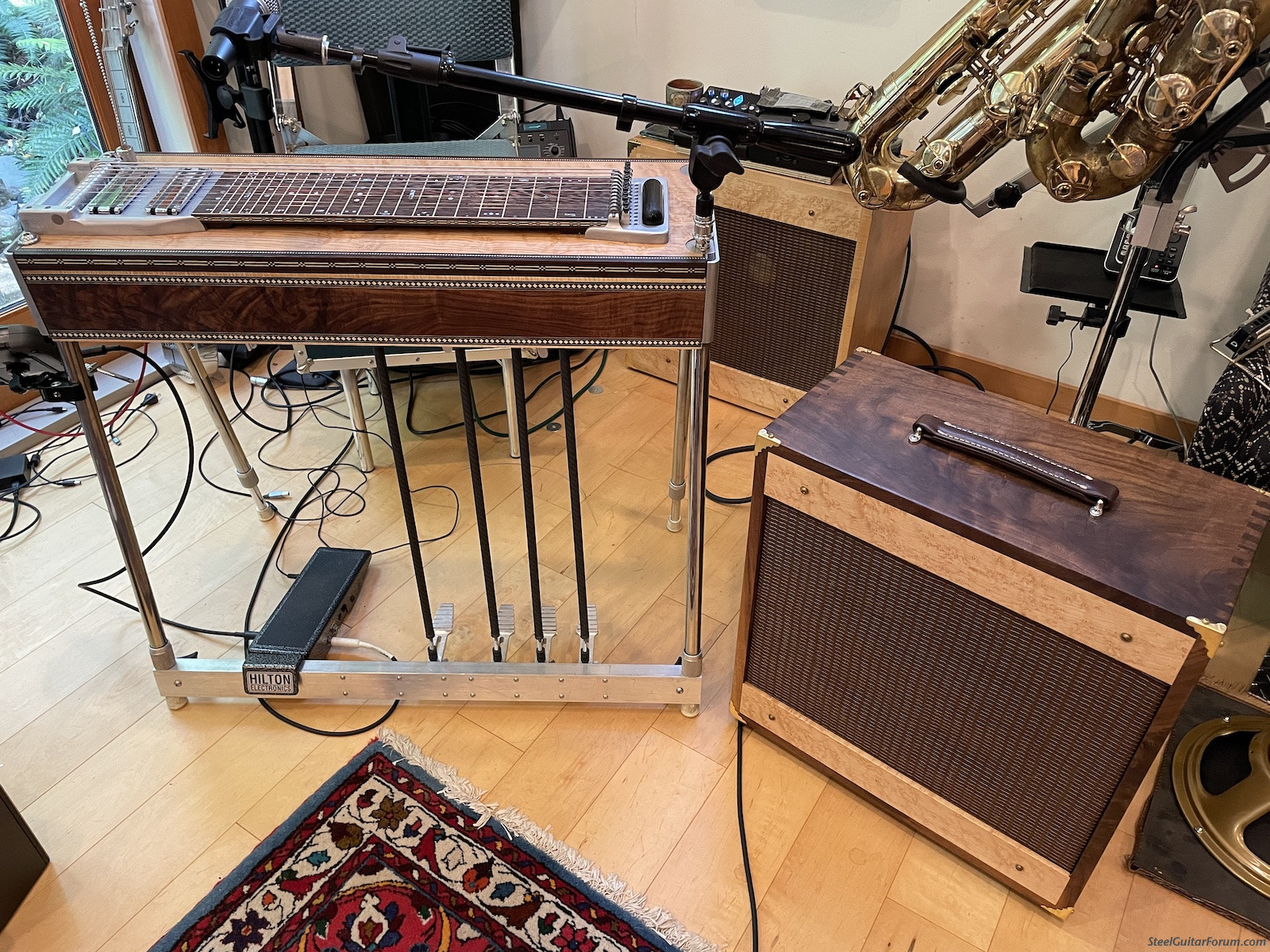
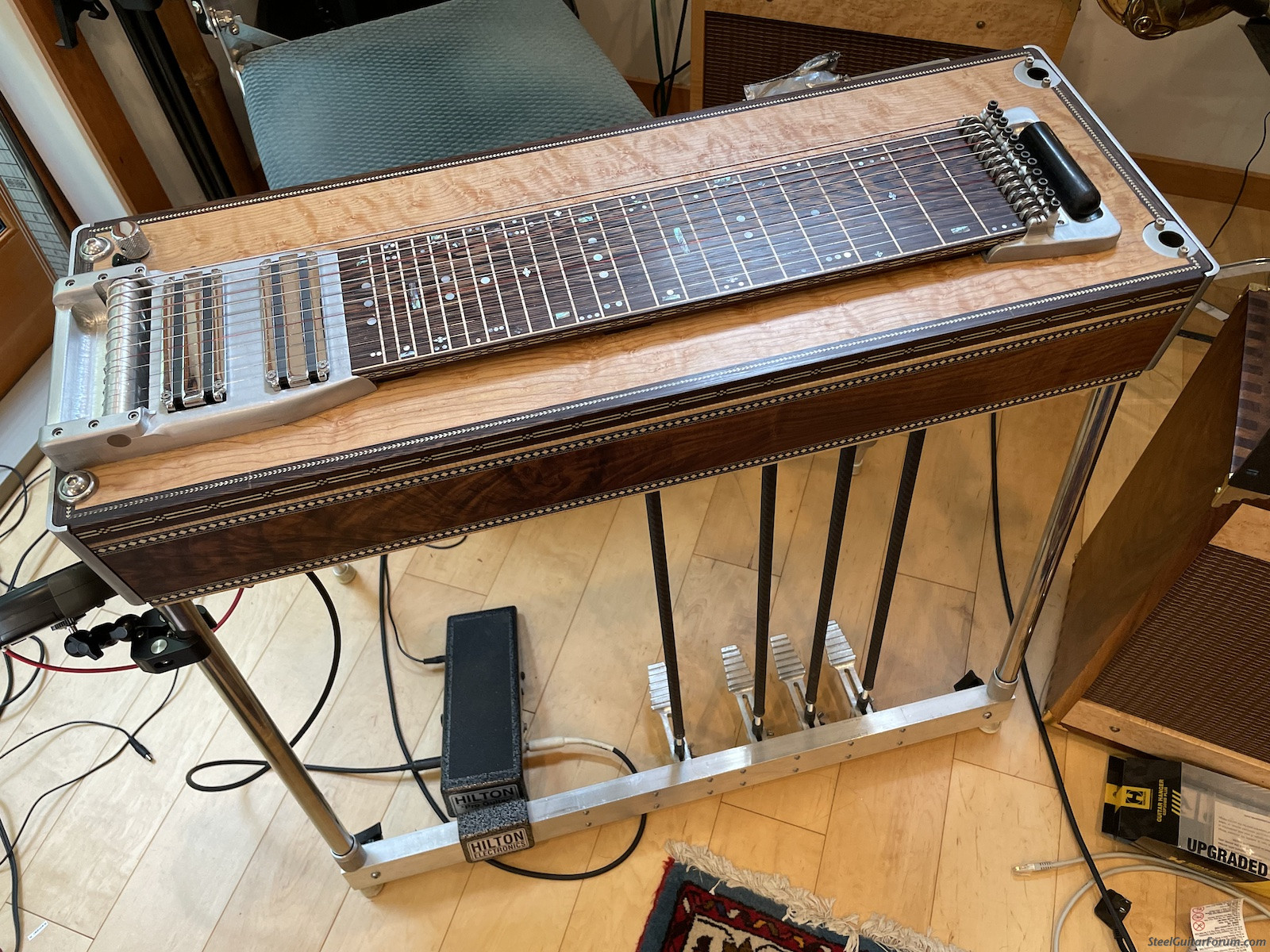
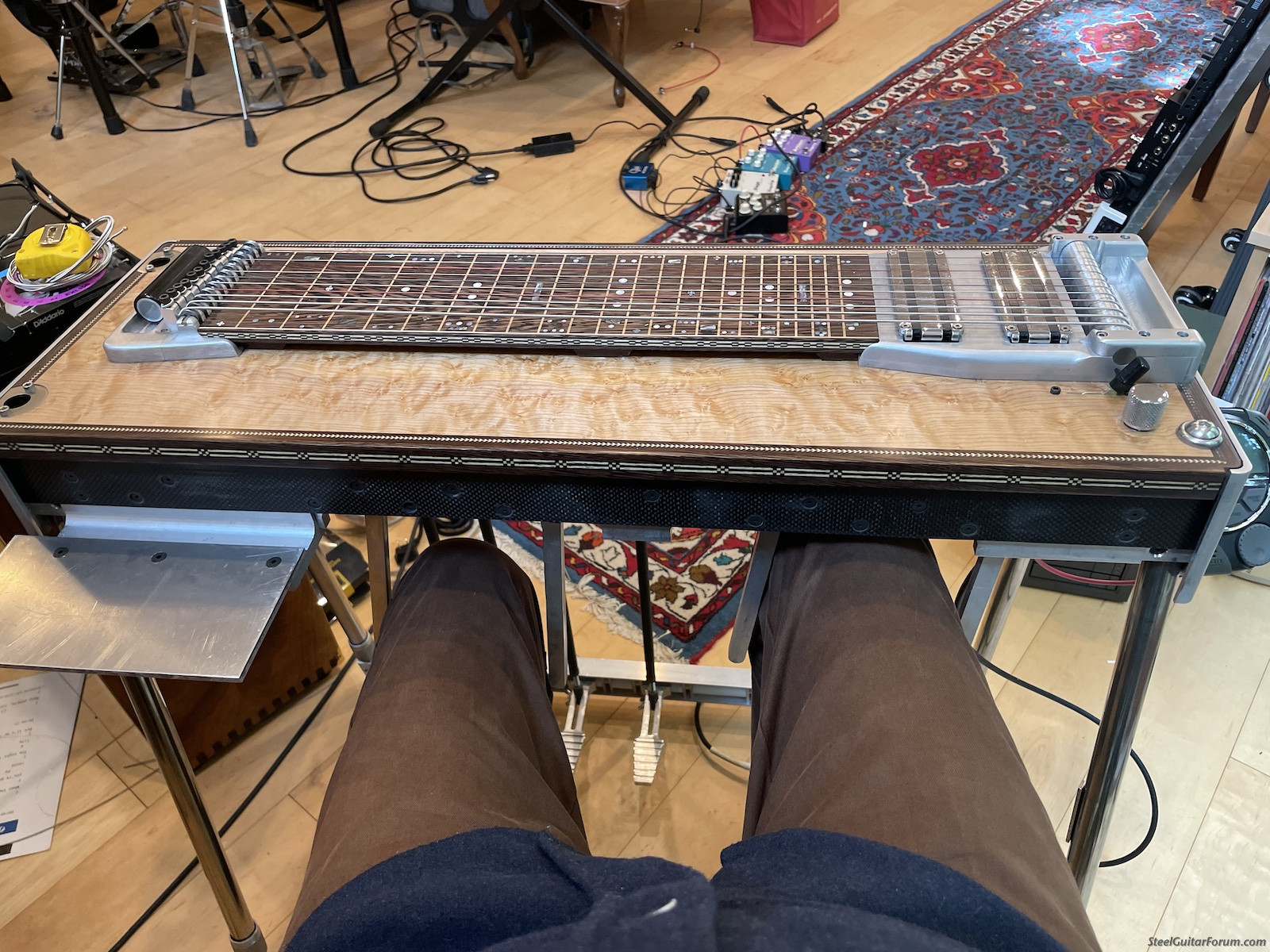
The Steel Guitar Forum Store
Visit Our Catalog for Strings, Instruction, Music and Accessories |
Send a Donation
Steel Guitar Links |
Moderator: J D Sauser
I need to rethink what my little mill is capable of! I should probably try to upgrade my cutters and fit some kind of DRO to my little mill. Or maybe just upgrade my machine. Then I could maybe stop doing a machinists work like a woodworker.Les Ford wrote:There are no castings in this guitar Tim. Everything is milled out of 6061 aluminum on my hobby mill, table saw and band saw.
That is a respectable end mill and pile off chip ! Those combo machines are cool. A bit of a compromise, but for the weekend machinist, more than enough obviously. I have been itching to buy the Grizzly combo 12" jointer planer. A compromise, but I would love to get rid of 2 of my machines for 1 that weighs less than 1/4 of just my planer. At some point I will be moving into a new space and upgrading some of my machinery and something like that may make more sense. Till then I am gonna try to fit some cheap DROs to my old mill drill. It will certainly be better than using a ruler!Les Ford wrote:
Tim, here is my setup:
![]()
I use the rotating table as a spacer to get closer to the cutter and to cut angles. It also makes it easier to adjust the tramming.
Hey JD,J D Sauser wrote:some amazing woodwork and machining!
How's that Neck Pickup acting?
Thanks!... J-D.
Les Ford wrote:Hey JD,J D Sauser wrote:some amazing woodwork and machining!
How's that Neck Pickup acting?
Thanks!... J-D.
I mainly use the neck pickup, so it is working pretty well but I might swap it out for a 12 string Stringmaster style pickup that a buddy made for me.
I'm thinking to try to mill the changer/pickup assembly to support a plastic pickguard so that I can try different pickup combinations because I want to get away from these super high output steel guitar pickups.
J D Sauser wrote:Les Ford wrote:It does exactly what you would expect. It has the warmer tone typical of a neck pickup.J D Sauser wrote:
What I was wondering Les, is what it sounds like (the “neck” pos. pickup).
I have been wanting to add a neck-pickup to my guitars for a long time to “warm”- up the tone.
Thanks!… JD.
Some people like a thinner sound but for me the neck pickup is better no matter what type of pickup it is.
Les Ford wrote:J D Sauser wrote:Thanks for confirming that it does what it's supposed to do.Les Ford wrote: It does exactly what you would expect. It has the warmer tone typical of a neck pickup.
Some people like a thinner sound but for me the neck pickup is better no matter what type of pickup it is.
I am studying how to get the thin string only to warm up with a neck pickup only under these. I like "clear" bass strings but warm high strings without deadening the bass strings.
And I should maybe specify that I am thinking C6th or Universal, where string gauges can range from o.o11 thru o.o70 all using the same scale length. It's a challenge.
I would like to have 4 pickups, under string 1-5 or 1-6 and another under string 6-10 or 7-12 respectively (10 or 12 string) on both the bridge and neck position and being able to balance them all previous to bundling the signal sent off to the amp.
I am currently modifying changer on several guitar with the same goal of "pre-EQing" the sound ACROSS the strings, using different shapes and materials on the changer fingers, and it's been a big step forward to that goal.
I like to pick at or right of the 24th fret on C6th for pick-to-string response and also a more constant tone, on E9th I would probably even be more over the 26th fret. But that with the bridge pickup only, brings about a nasal sound we often have tried to "thicken" by adding "bottom" via boosting the low end on way too powerful amps.
Your guitar has evidently many "Ross Shafer gen. SIERRA"-elements which are worth while considering since the company has again led the way in new ideas being incorporated. Very well built, beautiful metal and wood work, which is a rarely found combination on one-off's. So my hat to you!
One more question. I just got me a mini-mill and am looking for good end-mills for aluminum. I see your end-mill bit looks quite unique. IF that one seems to do uniquely well cutting aluminum as it looks, would you mind sharing what brand it is (where to get it), because that Chinese-Amazon junk is sucking the daylight out of my nervous system.
Thanks!... J-D.
That confirms what I have been experiencing. Don't laugh, but router bits actually work pretty well, and can be sharpened pretty easily with a fine diamond stone. Smaller router bits under 1/2" not so good though. I think my machine doesn't spin fast enough for these.Les Ford wrote:Hey JD,
I've worked out that you want to avoid any kind of coating on your end mills and to get the ones with only two flutes. Coatings and extra flutes seem to gum up with the aluminum.
Thanks Les.Les Ford wrote:Hey JD,
I've worked out that you want to avoid any kind of coating on your end mills and to get the ones with only two flutes. Coatings and extra flutes seem to gum up with the aluminum.
I only buy American or Canadian made end mills if I possibly can with the exception of round over mills, which are ungodly expensive, so I get those from Accusize, which I think is a Canadian reseller of Asian tooling. I like the Niagara Cutter brand, but anything made in North America tends to be higher quality and lasts longer before sharpening.
You can save a lot of money by looking around on Craigslist for used American tooling.I have bought bags of end mills and lathe tooling from retired machinists. I bought all my lathe tooling for five bucks each from one fellow who also had some cool custom made cutters that he had made himself. You can literally by them this way cheaper than you can sharpen them, and they tend to be good quality cutters.
That big cutter in the photo I posted is one of these: https://www.amazon.ca/dp/B00GWQ55I8?ref ... asin_title
I got it for a specific job in making some new end plates but it has turned out to be generally useful.
I'm dealing with some of the same issues as you. I am experimenting with a 12 string guitar tuned down to A6 with a Bb on the bottom and I am having to use Bass VI strings on the bottom couple of strings to try to get them to not be too rubbery. I'm going to try a 13 or 14 string guitar next and break out the bottom strings from separate pickups to a separate output and into a separate pre-amplifier and separate sides of a stereo Seymour Duncan Powerstage. This way I can have not have delay and reverb muddying up the bass.