Page 1 of 1
How to cut sheet steel for changer scissors
Posted: 20 Aug 2022 8:26 am
by Les Ford
Any ideas on the best way to make the parts for the scissors in an all pull changer? They are fairly complicated; needing the half inch hole for the axle, the corresponding rounding of the top to match the fingers, the bent tabs with the holes for the pull rods, the drilled return spring extensions and so on.
I was looking at cutting these shapes out on the bandsaw but they are pretty fiddley for that approach. Are these parts usually stamped out before bending?
I'm trying to find a way that maximizes my chances of keeping my fingers.
Can be cut on a Band Saw
Posted: 20 Aug 2022 2:13 pm
by Andy DePaule
Hi Les,
They can be cut on a Band Saw, but you should get a metal cutting blade.
Before cutting the sheet steel, Copy some drawings of the parts and glue them onto the sheet metal.
Center punch all the holes and drill them first on a drill press.
Then after that remove any rough edges with a file.
Doing the bend is easy if you get a "Steel Break". I got my 18" break from Harbor Freight for about $40.00 and it does a good job with little effort.
As for getting the top edges rounded nicely. I would make a jig with an axel the same size as the axel hole size. Clamp it to a disk sander table base and rotate the parts one at a time agains the spinning sander disk.

Posted: 24 Aug 2022 7:43 pm
by Bobby D. Jones
If you use a bandsaw to cut your parts, Use Paraffin Wax or Bee's Wax rubbed on both sides of blade for lube. It will cut much better.
When drilling thin metal sheet, Be very careful and use Pliers or Vice Grips to hold the piece, If the drill grabs as it goes through the sheet metal, It can fold, twist and wrap around the drill bit and take your fingers into a dangerous situation.
Worked in a machine shop, Shop owner had a missing finger from a drill press and thin sheet metal accident.
Good Luck On Your Build.
Posted: 24 Aug 2022 9:07 pm
by Ian Worley
The steel scissors on most production guitars are made with a punch press. A tool maker fabricates a custom die for each piece in the correct shape and the shop can punch out a big pile of them at once, holes and all, flat, consistent shape, nice clean edges. It's not something you can easily replicate with common tools in a home shop. That leaves you with the more crude methods described, bandsaw, grinder, file, etc. As Bobby suggests, that approach can be a really good way to slice the crap out your finger(s) so be very careful.
You might consider using 1/16" 6061 aluminum angle instead to fabricate the scissors. It's not going to be as durable over the long haul, but much easier to work and achieve clean and consistent results with more basic tools.
Another note if you haven't disassembled a PSG scissor before, but the halves are typically joined with what is called a "shoulder rivet", which has thicker "shoulder" section in the tenon adjacent to the head and slightly longer than the thickness of the scissor material. One half of the scissor has a larger hole that corresponds to the diameter of the shoulder. This provides a small amount of free play for that scissor, so it's not squeezed up tight against the other piece when the rivet is cinched up. If you're not able to find the correct size shoulder rivet you can just use rivets with straight tenons and fabricate some small bushings to slide over the tenon and serve the same purpose.
Ian is right, but...
Posted: 25 Aug 2022 6:15 am
by Andy DePaule
I agree. Ian is right, No question about it, but most people on this thread will not have access to a punch press or tool and die maker to fabricate these parts.
Even if you did have someone like that available, the cost would be quite high.
There is another alternative less expensive and risky way. Have the 1/16" (1.5mm) sheet steel laser cut to shape. The laser can also make the needed holes.. You would need to provide the drawings.
I get my steel fretboards and other metal parts cut by laser at a sign shop.
Most trophy shops can also do some of these things.
Bobby had this very good advise: "If you use a bandsaw to cut your parts, Use Paraffin Wax or Bee's Wax rubbed on both sides of blade for lube. It will cut much better.
When drilling thin metal sheet, Be very careful and use Pliers or Vice Grips to hold the piece, If the drill grabs as it goes through the sheet metal, It can fold, twist and wrap around the drill bit and take your fingers into a dangerous situation".

Re: Ian is right, but...
Posted: 29 Aug 2022 8:58 pm
by Ian Worley
Andy DePaule wrote:...but most people on this thread will not have access to a punch press or tool and die maker to fabricate these parts.
Even if you did have someone like that available, the cost would be quite high...
...that's the point...
Thanks Ian
Posted: 30 Aug 2022 9:24 am
by Andy DePaule
Thanks Ian,
Hope you didn't think I was knocking what you wrote because I know you were on point and right.
It would be nice if someone who had the dies for a good changer design would have a bunch stamped out for sale.
I imagine the market for them would be very limited.
Andy
Thanks Guys
Posted: 30 Aug 2022 2:23 pm
by Les Ford
Ian Worley wrote:The steel scissors on most production guitars are made with a punch press. A tool maker fabricates a custom die for each piece in the correct shape and the shop can punch out a big pile of them at once, holes and all, flat, consistent shape, nice clean edges. It's not something you can easily replicate with common tools in a home shop. That leaves you with the more crude methods described, bandsaw, grinder, file, etc. As Bobby suggests, that approach can be a really good way to slice the crap out your finger(s) so be very careful.
The parts that I have seen look like they have been stamped so this certainly makes sense.
Water cutting sounds like it might be a good idea. I'll try to price that out and see if it's doable. Otherwise I'll try to come up with a fixture/jig to help me cut these things without losing any fingers. Hand guiding those cuts just looks dangerous to me.
I like the aluminum idea. I'm thinking that there might be issues with wear on aluminum parts but the lighter weight of those parts might make for a more lively tone from the bridge/changer assembly.
Good thought Les...
Posted: 30 Aug 2022 6:58 pm
by Andy DePaule
Good thought Les,
Please post what you find out about the cost of doing it that way.
I'd completely forgot about that method of cutting steel.
Good luck to you and to us all on that,
Andy

Posted: 31 Aug 2022 8:59 am
by Scott Swartz
If you have the capability to produce dxf files (ie from AutoCAD or other CAD software), there are lots of laser cutting places who could easily make the scissors and even add the bends, for example
https://sendcutsend.com/
$29 minimum order and lots of available materials
I agree with the safety thoughts of everyone above on trying to cut then on a saw, especially compared to the ease of uploading a dxf and having them appear in a couple weeks.
Could maybe even laser cut the control fingers although the laser cut edge surface would need finishing for string contact area, shaft hole reaming, etc.
Waterjet Cut Parts
Posted: 28 Sep 2022 8:42 am
by Les Ford
I ended up going with the water cutting option at a fabricator in Nanaimo, which is close to me. The cost in Canadian dollars was 8 dollars for each set of two parts for each string.
I just made up the drawings in Adobe Illustrator and exported them as Dxf files for the cutter.
Something to be aware of is that the two larger holes for the rivet and the shaft have to be drilled out to clean them up to size. It looks like the cutter software is doing some kind of compensation for the cut line. This is a good thing because it gives a chance to remove any burrs and avoids the hole being oversized due to the kerf of the cut.
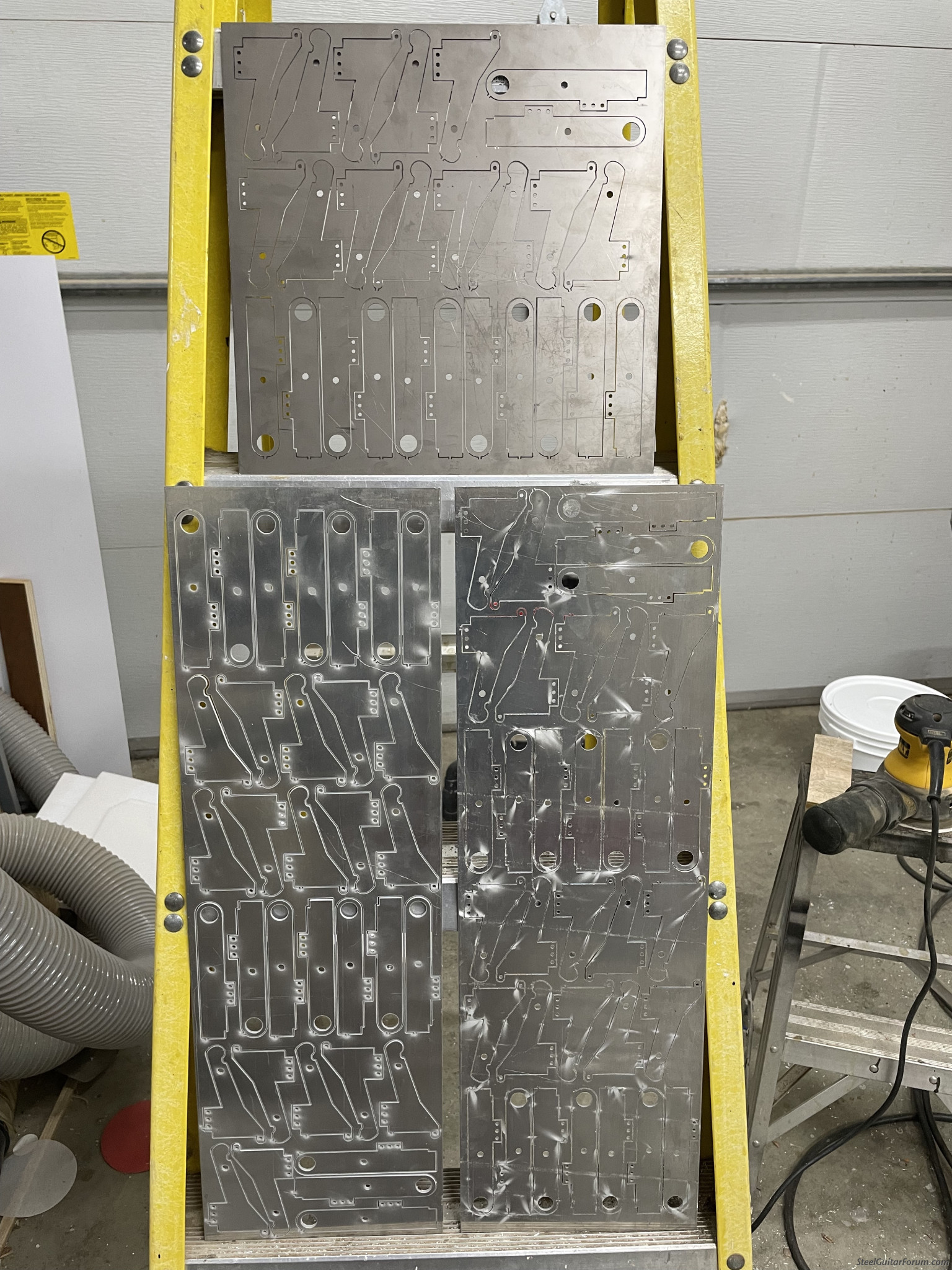
Posted: 28 Sep 2022 8:51 am
by Ross Shafer
lookin' good!
Thanks Ross
Posted: 28 Sep 2022 3:01 pm
by Les Ford
Ross Shafer wrote:lookin' good!
Thanks Ross, You have been a complete inspiration to me. Your guitars are on a whole other level.