Page 2 of 3
Posted: 5 Dec 2016 8:16 pm
by Stephen Williams
Erv, seems like your comments are a variation of shut up and dance......i.e. shut up and play.
But what about when i can't play? i'm lying in bed and gotta have something to think about eh? PSG axle stress.
Posted: 5 Dec 2016 8:25 pm
by Stephen Williams
Doug,
Even though there are 10 point loads on the axle about 11/32" apart, it is equivalent to a Uniform load. The length between supports at ends in my case is 3.75". This is correct length for Bending Moment. The resultant force on the axle is a horizontal force pulling it towards the nut.
You might well be right that forces are higher than 25lbs. i just used the lower numbers and still came out overstressed! And when a string gets pulled the forces are higher but not quite sure how much. The force of the bar is very little because it hardly changes the pitch of the strings.
All this is to say is that building Musical instruments is a combination of art and science. In this case the axle might be at it's limits but who knows? maybe it'll sound better. We'll see.
Posted: 6 Dec 2016 8:49 am
by Erv Niehaus
Stephen,
I think you've got that right!

Time could be spent in a more beneficial way, like playing that combination Singer sewing machine and electric cheese slicer.

Posted: 6 Dec 2016 2:27 pm
by Carl Mesrobian
@John Billings - I tend to think it would make a difference but have no scientific proof, just "a feeling deep inside, oh yeah!"
I'd stop stressing and just play the thing
I think about this kind of stuff when walking the dogs (and they are thinking of squirrels).
Posted: 6 Dec 2016 2:34 pm
by John Billings
Carl,
A pedal steel is the sum of it's parts. Those old ShoBuds are famous for their sound. Discounting changer axle diameter? Well that might be an important part. At Performance, we used 1/2" axles.
Posted: 6 Dec 2016 2:38 pm
by Carl Mesrobian
Stephen Williams wrote:Erv, seems like your comments are a variation of shut up and dance......i.e. shut up and play.
But what about when i can't play? i'm lying in bed and gotta have something to think about eh? PSG axle stress.
You need to get out more
John - I don't discount any part of the signal chain..
Posted: 6 Dec 2016 3:10 pm
by Georg Sørtun
Erv Niehaus wrote:Georg,
If we're nearing the stress point for steel, there's no question in my mind that what's needed is titanium for changer axles. You should know that!

I do know that titanium is
not as hard and stiff as the most hardened steel, so I long ago ruled out Titanium as suitable material for PSG-changer axles
What I noticed - after much testing and retesting back and forth between the original axle and the "super hardened" axle (with all else the same) - was that the original axle vibrated with, and sucked up some of, the string-vibration, resulting in a slightly less precise tone-frequency and a noticeable and measurable loss of sustain. To me the audible difference in tone and sustain, mattered enough to go for the new, "super hardened", axle.
How this would play out on other PSGs, I have no real knowledge about, as I have only modified this particular Dekley. I have however had the chance to compare its improved sustain capabilities with Mike Sweeney's Zum on one occasion - as I took lessons from him at his place, and the old, modified, Dekley kept singing with a perfectly clear tone long after Mike's steel had died off completely. That at least tells me "something".
Posted: 6 Dec 2016 5:47 pm
by John Billings
Some metals are better sounding than others.
Posted: 6 Dec 2016 6:19 pm
by Donny Hinson
Georg Sørtun wrote:
...The body itself is rarely ever the problem when "body drop" is noticed - the average PSG body doesn't flex much. It is almost always the parts where the strings are attached and pedal-pulls are applied, that are not attached well enough to the (pretty rigid) body to take up the variations in tension without moving.
Advice: look at connections between parts and the body, before blaming the body of not being rigid enough.
Georg, my experience is different, and I find that
most bodies will deflect enough to easily show up on a tuner. You can take just your thumb and press down hard in the center of a guitar, and see a deflection on the meter. Likewise, when you push a pedal, you're pulling the front apron (and whole cabinet) slightly downwards. Why else would this "cabinet drop issue" seem to be a problem mostly when the foot pedals are used, but very seldom when knee levers are used?
Inquiring minds would like to know.
Posted: 6 Dec 2016 8:15 pm
by Georg Sørtun
Donny, although there are some weak PSG bodies around, that is not "the rule" in my experience.
Nearly all pull from pushing down a pedal, gets redirected to increasing the string tension - unless you push the pedal so hard that you pull really hard on the pedal-stop in the front apron and thereby twist the body ever so slightly. Audible detuning of non-pedaled strings will happen before you hit the pedal-stop, because most detuning is related to change in string tension, not to where the pedal is attached to the body.
In reverse: if you for instance have a B to A lower on 5th and 10th string, you release string tension. Then you will in most cases be able to hear, or at least measure, that a non-pedaled 6th, or the 7th, string raises slightly.
The changer is fastened on a relatively small area of the top plate on most PSGs, and with a couple of hundred punds of tension on top and very little down on the scissors, the changer gets pulled slightly in/over on top. This is what my "light and mirrors" measurements have told me - both on the old Dekley and on other PSGs I have acquired later, and when counteracted by a stronger, stiffer, changer structure that covers a larger surface on the top plate, the deflection - audible and measurable "body drop" - is greatly reduced.
When in addition the changer axle is prevented from giving - bowing - under string tension, nearly all detuning is eliminated even for the weakest of bodies.
So, yes, you are right, a PSG body does bend a little under pressure, but that is in my experience a minimal problem compared to all the other parts that give and bend under varying string tension, and it doesn't take much to become audible.
Posted: 6 Dec 2016 8:57 pm
by Jerry Jones
Could you not tune the A and B pedaled pitches at the keyhead and determine if pedal pressure is involved? Seems you could also repeat the same experiment with three dial indicators, one on each pillow block and one at a center location along the axle. Once again with no pedals involved, just increased string tension on 3, 5, 6, & 10.
Posted: 6 Dec 2016 9:04 pm
by Georg Sørtun
Jerry Jones wrote:Could you not tune the A and B pedaled pitches at the keyhead and determine if pedal pressure is involved?
Done that ... pretty much the same detuning effects as with pedal pushing. Slight differences contributed to how the balance in the changer is affected by pulling on scissors.
Posted: 6 Dec 2016 9:44 pm
by Roger Shackelton
Has anyone checked the detuning of a Fender 800 or 2000 PSG?
Roger
Posted: 8 Dec 2016 9:54 am
by Dave Greene
Reaction force in axle depends upon string material, and whether plain or wound. Also, reaction force in axle depends upon whether tuning arm is supported by a push/pull rod or merely a stop.
Also, hopefully the axle rod is Stainless Steel with an Fy of 50 ksi. It still may be slightly overstressed using 0.6 x Fy = 30 ksi. It might also be a SS rod with a higher yield than 50 ksi. Interestly, deflection at mid point calculates to be .011". You'd think that might bind the levers
I was a structural engineer in life and a wanna-be PSG player. PM if you want to discuss more.
Posted: 8 Dec 2016 11:55 pm
by Stephen Williams
Dave. I got it slightly wrong. In my case the axle force was actually 33lbs not 25lbs. I need to draw a diagram. But that means stress is up to 50ksi. either the steel is stronger than advertized or 25lb pull is too much.
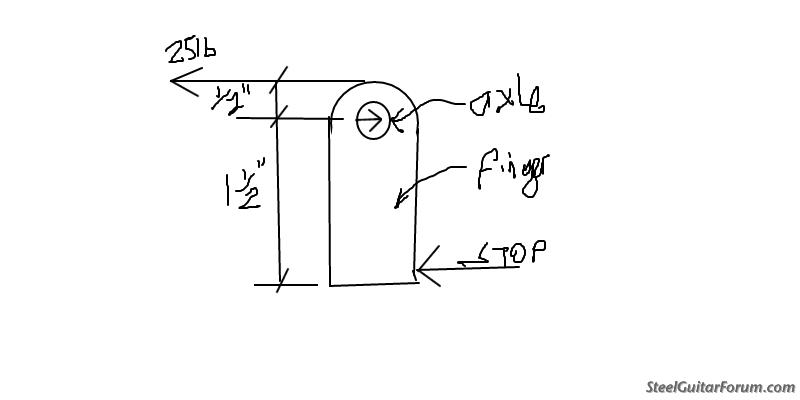
Herb Remington....turtle
Posted: 14 Dec 2016 11:02 am
by Tommy Huff
hi Members. I believe Herb Remington and probably Bobby Bowman was involved.....had a piece on the back of the changer..it was part of the changer with a brackett running to the center of the shaft to help eliminate flex not sure if it was sucessful......anyone familiar? it was called the turtle I believe.....I owned a Remington for a short time.
Posted: 14 Dec 2016 11:51 am
by James Collett
The concepts here are correct, although there is more at play here. From an engineering standpoint, I would do the calculation both with a distributed load, and then using point loads, as the real answer is somewhere in-between, and both solutions will give you different "critical" data components. What's important to remember here is (1) maximum bending stress is calculated at the top or bottom (most critical points, one in tension, the other compression) of the rod at the place with maximum bending moment (in this case the middle, lengthwise). Stresses then taper off from there, meeting at 0 in the dead center of the rod. See picture (nptel.ac.in)
Once yielding occurs, the parts of the section that have yielded now behave plastically (that is, they deform in order to maintain strength). The stress=M/s calculation no longer works, as everything in excess of the yield stress stops there... but let's not go down that rabbit hole.
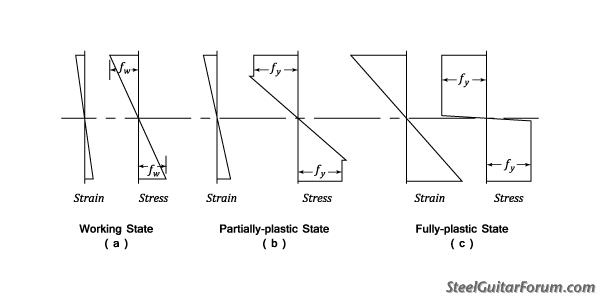
(codecogs.com)
One thing that's important to note is that the equation used, M=wL^2/8, is for simply supported beam elements--that is, in this case, the ends are free to rotate as the axle flexes. I know most pillow blocks at each end of the changer axle are somewhat thick, and would resist the ends from rotating, thereby imparting some "backwards" moment on the ends of the axle. This would reduce the maximum moment in the axle (in ideal conditions, M_max=wL^2/8-w*L^2/12), which, in this example, would probably prevent the axle from yielding. Look up "Fixed End Moments" if you're curious.
Posted: 14 Dec 2016 12:02 pm
by Erv Niehaus
I'm getting a headache.

How did we go from a good ole three chord country song to this?

Posted: 14 Dec 2016 12:40 pm
by Dave Greene
Jim:
Thanks for the comprehensive look. I believe the only rotational restraint (axle torsion) at each end would be from friction of the axle in the mount.
I did the calculations using tension forces on each string assuming D'Adario string gauges and came up with nearly the same maximum bending moment as using a uniform load.
I had a structural engineering practice for 30 years, and was licensed in 12 states (including CA).
My biggest problem is playing my PSG at 81

Posted: 15 Dec 2016 7:29 am
by James Collett
Hi Dave,
My reference to rotation was not torsional rotation, but rather rotation due to bending. While not enough to be fully fixed, there is some moment resistance provided by the pillow blocks on each end of the axle--so the true solution lies somewhere between fixed end and simply supported.
Posted: 15 Dec 2016 8:44 am
by Georg Sørtun
Erv Niehaus wrote:I'm getting a headache.

How did we go from a good ole three chord country song to this?

Well, it's all related to the same instrument

Posted: 15 Dec 2016 9:37 am
by Erv Niehaus
There is quite a difference in the complexity, however.

Posted: 15 Dec 2016 9:48 am
by Georg Sørtun
The math maybe (I'm not strong at math, so I prefer to measure on the real thing), but the rest is just different sides of achieving the same thing - making music.
Posted: 15 Dec 2016 10:12 am
by Erv Niehaus
I think we're approaching the realm of paralysis by analysis!

Posted: 15 Dec 2016 11:19 am
by Georg Sørtun
One shall never stop questioning ... everything
