Page 2 of 4
Posted: 5 Mar 2014 5:27 pm
by Mickey Adams
Why do you think I got this??????...Im thinking Buck Reid and I will do just that as a team!!>.
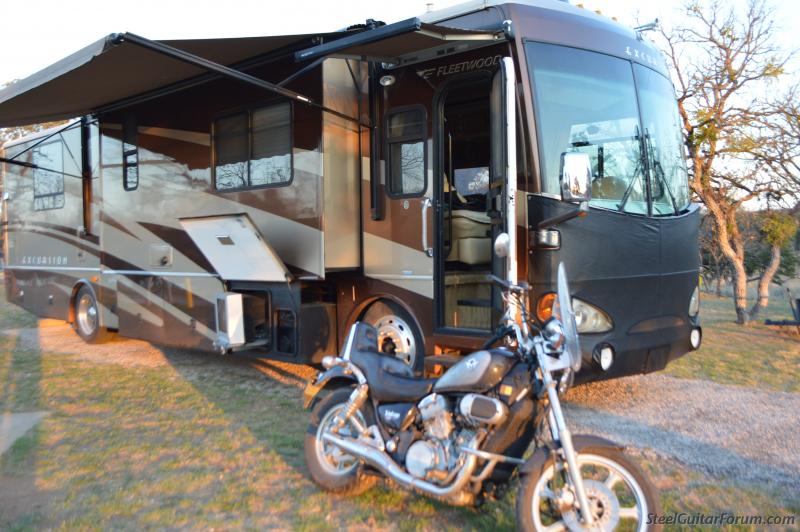
Posted: 5 Mar 2014 5:35 pm
by Dustin Rigsby
Is that a Yamaha Virago ?
Posted: 5 Mar 2014 7:23 pm
by Mickey Adams
Kawasaki Vulcan 750
Posted: 5 Mar 2014 7:34 pm
by Rick Barnhart
One pedal, three levers.
Posted: 5 Mar 2014 8:57 pm
by Scott Denniston
Well sorry to dissent. I think a Cnote is a bit steep for your average steel player in these times. We don't have no fancy bikes or RVs. I mean, the rest of us. I really think you'd make a lot more off the production and actually help several times more people by making it accessible. Oh say $35 or $40. Heck I might even buy one. Very useful. Otherwise I guess I'll get by like always. Again, sorry to dissent but that's just my honest feedback. I think some people have an idea & think "man if I sell 50 that'll be $5000. Worldwide I'll probably sell 400 the first month--$40,000.....etc." I don't think production is THAT expensive these days and frankly I'm just ever so slightly offended. Think of all those wonderful Jeff Newman tapes that taught us all so much. He did pretty well with them but what did they cost? Everyone could buy them & still feed their kids. Of course if your just targeting the retiree hobbyist market, more power to yuh. I don't mean to just be a ball of negativity but I hope you get my point. Now I see some incoming so I'll just duck outta here. But you did ask.----Scott
OOPs--oh I see this was all a spoof. Got Me!!
Posted: 5 Mar 2014 11:23 pm
by Tony Glassman
Scott, most people pay between @2000-$5000 for a steel guitar (not to mention vol pedal, amps, cords, bars etc.). Another "C-note" is a small price to pay to learn how to maintain, repair and optimally set one up. The price to ship a guitar to have some one else work on it (not including the actual repair charges) is probably pretty close to his asking price. Having built, rebuilt and repaired steel guitars since the mid 70's, I can tell you that the time involved to conceive, plan and execute a manual of this type is not insignificant.
Also, I don't see how you can insinuate that Mickey is in it for sheer profit. Check out the many free "YouTube" instructional videos he's produced and you'll find that he has been more than generous w/ his knowledge and time.
Posted: 5 Mar 2014 11:43 pm
by Lane Gray
Scott, I bet that, if Jeff had done a video of the scale and scope of Mickey's proposed project, in 2014 dollars, it'd probably cost the same $100. Remember we've not seen a new video from Jeff in nearly 20 years of inflation...
Posted: 6 Mar 2014 12:09 am
by John McClung
Topic ideas, Mickey: raise helper springs, what they are, how to use them; what are return helpers (I actually don't know, bet I'm not alone)splits with screws or rods; how to remedy "over-cranked" pull rods; proper pedal height and how to adjust for that; how to assess whether your steel is the proper height for your body; the use of compensators; how and where to lubricate your steel, and how often to do it; best ways to clean strings; fastest way to change a set of strings; proper setup of the E9 second string half stop using string 9 lower to accomplish that. Get busy!
Posted: 6 Mar 2014 12:33 am
by Peter den Hartogh
Mickey
Why don't you write a script outline proposal (without details) which will end up in a "blue-print" plan for the whole complete project, which could be presented to the forum(s) with a poll for amendments.
That way you can set up a business plan because you can gauge the size of the project.
This would be better than starting somewhere and filming whatever you're doing. It would also avoid omissions.
You might want to create 3 DVDs: All Pull, Push Pull and Single Fingers. Each DVD could include a list of common mistakes and their fixes.
Just thinking out loud.
Posted: 6 Mar 2014 7:27 am
by Dustin Rigsby
Mickey Adams wrote:Kawasaki Vulcan 750
Up here in the Great Lakes, were only dreaming of scooter weather â™ ï¸â™¥ï¸â™£ï¸â™¦ï¸!
Posted: 6 Mar 2014 7:51 am
by Willis Vanderberg
I have paid a heck of a lot more than a hundred bucks to send guitars to Mike Cass and Albert Johnson. Maybe a hundred is a lot but in the grand scope of things it is relatively small amount.You can just bet that this video will be well thought out and easy to understand.
I could write you a book on the so called experts who have screwed up more than one of my guitars before I learned to screw them up myself.
I consider myself pretty well up on my horns but still have a lot to learn.
The bottom line is , your guitar can be set up by you , the way it fits you the best. It really does make a difference in the way you play.
I hope the video can be encoded so it can't be copied...
Old Bud
Posted: 23 Mar 2014 4:06 pm
by Wayne Quinn
Please let us know when its available Mickey. like you say its a small price to pay compared to shipping prices to day. it would cost me 180.00 to ship mine to you. one way and besides I get to learn how to do my own work on my own babies and keep them home..

Posted: 23 Mar 2014 6:15 pm
by Dylan Keating
I would love a video like this.
Posted: 23 Mar 2014 6:39 pm
by Bruce Morrison
I don't even have a PSG, and yet I'm already worried about having an instrument I can't maintain myself (always have been able to in the past with regular guitars and basses). I think that pricing it any lower, given the number of units that are likely to sell (relatively low), would be a mistake. I mean... I am as cheap as the next guy, but you have to support the people who are supporting you.
Posted: 24 Mar 2014 6:25 am
by Alan Bidmade
A couple of subjects for consideration:
stripping/cleaning a changer (and re-assembling)?
creating tunable splits by means of screws as well as rods.
Posted: 24 Mar 2014 6:54 am
by Mickey Adams
I appreciate all of your input...I have finished the first two chapters.. Im afraid that it would be nearly impossible to cover ALL of the topics requested..This videos topic is re rodding, and reconfiguring. It is not a total tear down/rebuild video.. There just would be just too many things to cover for one disc. Im already at 42 minutes, and have not even gotten to the changer ratios/rodding portion of the video...
Posted: 24 Mar 2014 8:54 am
by Mike Wheeler
Posted: 24 Mar 2014 9:06 am
by Ollin Landers
Looks like there may need to be a two part set of DVD's. Either a beginning and advanced or just a Part one basic maintenance/set up and Part two advanced re-rodding and assembly.
You could do a 4 DVD set and never cover everything everyone wants.
I think the price is reasonable given the time it takes to produce the videos, edit, copy and distribute.
Posted: 24 Mar 2014 1:36 pm
by Niels Andrews
Posted: 24 Mar 2014 5:36 pm
by Mickey Adams
Ive been a pilot for 30+ years Neils...I can assure you...PSG did not pay for these..

Posted: 24 Mar 2014 7:35 pm
by Tom Keller
For the kind of information your presenting I feel your price is very fair. I doubt I could ship my guitar to a qualified repair person for much less than that.
Tom
Posted: 24 Mar 2014 8:46 pm
by Jack Aldrich
Keep us posted. I'll buy it.
Posted: 25 Mar 2014 8:41 am
by Dale Rottacker
Great idea
Posted: 25 Mar 2014 5:21 pm
by Steve Spitz
I think this would be a great product, something I could use. I can work on my steels, but not nearly as well as the best techs can, and for that reason, I've usually sent them out to the real gurus to get all I can out of my steel. I know any DVD alone can't replace the years of experience our top techs have, but it would be a great resource for most of us.
Mickey has been extremely generous with the teaching on the forum, I'd be inclined to support him, as I would to anyone else who does so much for us.
Cd
Posted: 8 Nov 2014 1:15 pm
by Kevin Barber
Just curious, what's the status of the dvd?