Page 2 of 3
Posted: 11 Sep 2010 9:21 am
by Pete Burak
Has anyone tried to tune out the cabinet drop using a 40" glue-clamp?
A quick trip to A-to-Z Rent-all...

Posted: 11 Sep 2010 11:14 am
by Bent Romnes
Tony Glassman wrote:I agree w/ an adjustable pre-loading truss rod running along the bottom of the deck from end plate to end plate, which would offset cabinet drop forces
wouldn't a pre-loaded (bowed) deck decrease the surface contact between the deck and necks and screw up vibration transmission.
Some people feel the pitch drop is due to changer axle flex rather than cabinet drop.
How much pre-loading are we talking here? 1/1000" of bowing in the middle? If so, a small amount wouldn't affect the neck/deck contact. Even if, it wouldn't hurt to leave the neck with a tiny gap like that. Imperceptible to the eye and held in place by screws.
Yes, Tony, I believe that some cab drop can be blamed on the changer axle/whole assembly flexing. But with a 1/2" quality steel axle and bolts thru the deck, I believe that this problem could be as good as eliminated.
I guess my lingering question is: How much of a bow do we need? 1 thou? 3? 4?
I also agree with what Chris Lucker said about having the pedal stops push upwards like on the Emmons. It makes sense..you push down on the pedal and flex the cabinet. Then the pedal crank hits the underside of the deck and makes an upward force to counteract the downward force from the pedal.
Posted: 11 Sep 2010 11:32 am
by mike nolan
Remember, we raise and lower strings. Most guitars exhibit a very small amount of cabinet raise when we lower strings because tension is released. Pre tensioning or back bowing the cabinet might exacerbate this.
A great opportunity for a bunch of cabinet raise threads.

Posted: 11 Sep 2010 11:37 am
by Rick Batey
Also, would removing all the strings to change them cause problematic upbow?
An argument for keyless and changing one at a time, of course. But mustn't get into that...
Posted: 11 Sep 2010 12:45 pm
by Storm Rosson

I think that the application of pre loading and use of tension bars/rods doesn't always result in real physical flex or movement in every situation, there is a static energy state that would result in a cumulative resistance against some of the variables that have been mentioned, as that's part of the whole pre-loading/torsion/energy equation I think...

Posted: 11 Sep 2010 2:29 pm
by Tim Heidner
Bob Hamilton, can you post some pics of your external truss rods?
Posted: 11 Sep 2010 4:36 pm
by Kevin Hatton
Cabinet drop is not a major factor on a properly built steel. You need to learn to tune around cabinet drop. Its not a big factor unless the guitar is poorly built. Still a solution would be useful.
Flex
Posted: 11 Sep 2010 7:21 pm
by Bob Hamilton
Hi Tim. Thanks for the interest, I'll try to get some pics up tomorrow. This method has worked for me on several steels. On guitars with significant detuning problems, I always look at the keyheads first, as Master Paul Redmond mentions, since a lot of tuning issues can be corrected there. Then I go for the truss rod. Doesn't matter if it's pedal pressure or string tension causing the problem, an additional upward stabilizing force on the cabinet is always helpful.
Posted: 11 Sep 2010 7:49 pm
by Tim Heidner
Thanks Bob, looking forward to it. I have this used guitar I bought as my first steel and it has a significant detuning problem so I'm looking for ways to fix it before I give up on it. I just took the end plates off today to see why the screws are loose and stripped, turns out the holes are real close to the edge of the apron and the wood is split, waiting for the glue and plugs to set up so I can try to fix it but not anticipating a whole lot of success.

Detuning
Posted: 11 Sep 2010 8:05 pm
by Bob Hamilton
Well the endplates need to be tight Tim, especially on the changer side. If there's any clearance available between the cabinet and metal at the changer end, it can cause tuning problems. I usually use feeler gauges at the changer end to check if it tightens against the cabinet as the pedals are depressed. This could definitely be part of the problem. It's usually a bunch of little issues in combination that add up to a sour guitar. BH
Posted: 13 Sep 2010 4:26 pm
by Pastor Bruce Kiser
What about a three-sided steel channel embedded
in the top of the deck facing downward attached with screws / and-or epoxy in conjunction with slightly thicker front and rear aprons ?
Pastor Bruce
Posted: 14 Sep 2010 11:47 am
by Richard Damron
Pastor Bruce -
You've hit the nail squarely on the head. A slightly thicker apron will increase the rigidity of the cabinet to a degree. To a further degree, the depth of the apron will greatly increase the resistance to bending.
The inescapable caveat: - Those things would have to be done during the initial manufacture of the instrument. Neither is a retrofit, which is the thrust of this thread.
Back to the drawing board.
Respectfully,
Richard
Posted: 14 Sep 2010 2:23 pm
by Storm Rosson

Richard, although I am entertaining a retrofit concept, all ideas including integral implementation should also be considered in this thread imho....Stormy

Truss
Posted: 14 Sep 2010 7:21 pm
by Bob Hamilton
Hi all. Lousy photos, but you get the idea here. These pictures are from ZB #1062. The rod is anchored at each end, as close to the strings as you can get, then over a knee crossrod or spacer to add upward thrust. Ugly but effective.
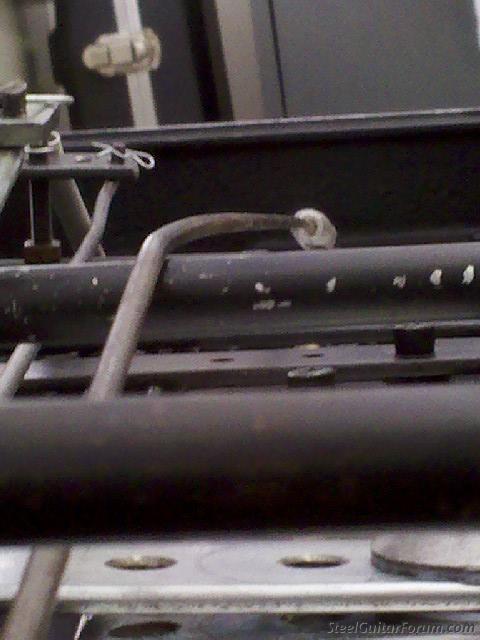
The arrow shows rod termination at the endplate.
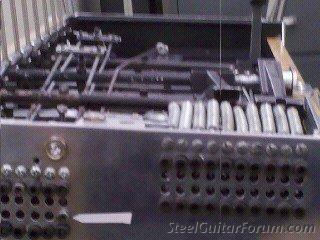
Posted: 14 Sep 2010 7:37 pm
by chris ivey
why not make the whole body out of heavy steel?
Posted: 15 Sep 2010 3:53 am
by Bent Romnes
You said it yourself Chris, because it's heavy.
Posted: 15 Sep 2010 4:23 am
by Jim Pitman
That's what I'm talkin bout Bob!
Thanks for the photos.
I wonder if we can get a few makers to consider the ideas in this thread.
Posted: 15 Sep 2010 4:30 am
by Jim Pitman
Pete - I tried the bar clamps on the end plates. It didn't make much of a difference on my guitar. I theorize it merely deflected the end plates in relation to the top at the end plate/top wood interface point. It might be effective on guitars that have more of a rigid end plate mounting design.
Posted: 15 Sep 2010 4:51 am
by Jack Stanton
Jim,
What you describe as a possible solution at the bottom of your fist post sounds very much like what I see when I look at the counterforce device on a Emmons Legrand III.
Posted: 15 Sep 2010 5:13 am
by Jim Pitman
Jack I had the impression the Emmons counter force mechanism used pedal actuation energy to counter detune. I had been told it stiffens the feel of the pedal action undesirably. Perhaps this is hearsay.
Can anyone else comment?
Posted: 15 Sep 2010 6:59 am
by b0b
What about the other sources of detuning? I've heard that a large component of "cabinet drop" isn't the cabinet at all, that it's flex in the changer axle and things like that?
Also, I've had several guitars where unaltered strings raise when I lower my E strings - a "cabinet rise" effect. An adequate solution should solve that problem as well.
Posted: 15 Sep 2010 8:04 am
by Pete Burak
Jim Pitman wrote:Pete - I tried the bar clamps on the end plates. It didn't make much of a difference on my guitar. I theorize it merely deflected the end plates in relation to the top at the end plate/top wood interface point. It might be effective on guitars that have more of a rigid end plate mounting design.
Jim,
That is so cool that you tried this.
I was thinking about how the Sierra Session Series legs have a long post that slides far into, and clamps into, a sleave in each corner of the endplates (the post is like 4x longer than the threads on normal legs).
I was thinking that the clamp could go on the Legs in a manner whereby bringing the legs closer together, flexes the body of the cabinet in opposition to cabinet drop caused by pedal pressing, string tension, etc...
An analogy would be... trying to break a piano bench in-half near the middle of the seat area, by grabbibg the legs on either end and pulling together.
Why does thinking about this stuff not only put a huge smile on my face... but actually cause me to start laughing hard out loud?
PSG Stuff... 'Love it.
Posted: 15 Sep 2010 8:41 am
by Jim Pitman
Pete - if thre's a guitar that might benefit from the clamp it would be the Sierra. They are built like a brick !@#!house.
Posted: 15 Sep 2010 9:00 am
by Curtis Mason
Has any manufacturer tried integrating the changer housing as part of the neck, and also including the bridge too. I can see where the changer being independent of the neck would allow for movement when a specific amount of tension would be applied to each string.
Also, I thought up an idea, and maybe someone has already implemented it, but...what if there were a "tension string" installed that would be pretuned/preloaded to a specific frequency, each would be different depending on the amount of tension needed to be released or countered...and as the string tension is increased on notes being raised, this tensioner string would be loosened to counteract the applied tension insuring that the same tension would always exist regardless of what strings are raised.
Just a thought,
Posted: 16 Sep 2010 4:25 am
by Tim Heidner
Hey Bob Hamilton, thanks for the pics. Does the pressure of the rod on the knee lever affect the way it moves any?